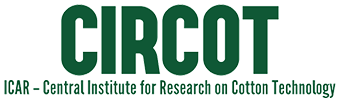
"The cotton is grown to be spun. If cotton spins well, obviously it is good, otherwise it is not!". These iconic words are of Mr. William Lawrence Balls, an eminent researcher, who can aptly be termed as the Father of Cotton Technology. These words also embody the nature and spirit of research work in the Mechanical Processing Division which began operations in 1924 and is the first and the oldest division of CIRCOT. The research and activities of this division have in many ways guided and charted the research direction of the Institute throughout its existence.
The cotton lint received in bale form from gin yards or cotton warehouses need to be subjected to a series of mechanical processing before it is converted into products like yarn / fabric. Mechanical processing of cotton starts with raw bales of cotton and process them in stages until it is converted into yarn or cloth. Mechanical processing Division of CIRCOT is equipped with state of art cotton processing machineries for undertaking research and development on various stages of mechanical processing of cotton. Mechanical Processing Division of CIRCOT also plays a key role in evaluation of spinnability of cotton samples received from breeding programmes under All India Coordinated Research Programme on Cotton (AICRP-cotton) and thereby helping cotton breeding program of the country.
Mandate of Mechanical Processing Division
Head of Division
Sr.No. | Name | Designation & Research Interest | Contact | Photo | |
---|---|---|---|---|---|
1 | Dr. N. Shanmugam | Principal Scientist (Textile Manufacture and Technology) Research Interest : Cotton fibre-yarn property modelling, Artificial Intelligence, Spinning sysyems, Cotton value chain, Natural fibre blends. |
Ext No. 301 | nshanmugham[dot]circot[at]icar[dot]org[dot]in | ![]() |
Scientists
Sr.No. | Name | Designation & Research Interest | Contact | Photo | |
---|---|---|---|---|---|
1 | Dr. Vishnu G. Arude | Principal Scientist (Farm Machinery & Power) Research Interest : Post harvest processing of cotton and natural fibres, ginning and spinning |
Ext No. 304 | vg[dot]arude[at]icar[dot]org[dot]in | ![]() |
2 | Dr. Senthilkumar T. | Senior Scientist (Textile Manufacture) Research Interest : Fibre composites, technical textiles and effluent treatment |
Ext No. 414 | senthilkumar[dot]t[at]icar[dot]org[dot]in | ![]() |
3 | Dr. G. Krishna Prasad | Senior Scientist (Textile Manufacture) Research Interest : Spinning, Technical textiles and Composites |
Ext No. 413 | krishna[dot]g[at]icar[dot]org[dot]in | ![]() |
4 | Dr. G. T. V. Prabu | Senior Scientist (Textile Manufacture) Research Interest : Cotton spinning, electro-spinning, nano application in textiles |
Ext No. 310 | prabu[dot]gtv[at]icar[dot]org[dot]in | ![]() |
5 | Mr. Himanshushekhar Chaurasia | Scientist (Computer Application) Research Interest : Machine Learning, Deep Learning, Image processing, & IoT |
Ext No. 221 | h[dot]chaurasia[at]icar[dot]org[dot]in | ![]() |
Technical Staff
Sr.No. | Name | Designation | Photo |
---|---|---|---|
1 | Mr.Sharad Vaman Kokane | Assistant Chief Technical Officer | ![]() |
2 | Mr. Santosh Vaman Kokane | Senior Technical Assistant | ![]() |
3 | Mr. Sanjay Gopal Phalke | Technical Assistant | ![]() |
4 | Mr. Yogesh Punnulal Nagpure | Senior Technician | ![]() |
5 | Shri. D. G. Gole | Technician (T-1) | ![]() |
Towards the end of the 20th century and continuing into this millennium, the Division diversified its activities and continue to carry out research work on blends of cotton with various natural and man-made fibres, technical textiles, nonwovens etc. Major technologies developed include:
Major achievements of the Division (Past and Present)
Agricultural Knowledge Management Unit (AKMU) of ICAR-CIRCOT supports information technology needs of the Institute by maintaining Internet Services, Email, Video Conferencing and other computer related facilities. AKMU also periodically updates Institute Website. AKMU also Local Area Network (LAN) and WiFi Network of the Institute. ICAR-CIRCOT is connected with 1000 mbps lease line under National Knowledge Network (NKN) provided by Govt. of India and 10 mbps ILL from RailTel to provide all the ICT services around the clock for the employees of the Institute.
AKMU provides server based enterprise class security to all the connected PCs for protecting the IT assets from malware threats and other external sources of threats. Institute internal IT assets are also protected using a state of the art Next Generation Firewall which protects from intrusion attacks originating from Internet.
AKMU manages ICAR-CIRCOT Website: circot.icar.gov.in. The website highlights research activities and achievements of the institute and act as an interface between institute and stake holders. The contents of the Institute Website are periodically updated with information on training programmes, recruitment of temporary staff, tender notices and other circulars of the institute. IP based video conferencing facility of ICAR-CIRCOT is operated and maintained by AKMU.
AKMU is also work closely with ICAR ERP, ICAR Unified Communication System and Government of India initiatives like Aadhar Enabled Biometric Attendance System (AEBAS) and Central Public Procurement Portal (CPPP) by providing technical support to end users of these systems.